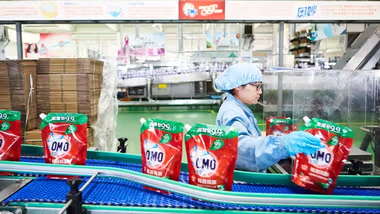
Safety at work
We want to grow our business responsibly. That means safety is not negotiable – it’s our number one priority.
Safety is about people
Facts and figures are important for measuring safety and driving progress, but they don’t tell the full story.
We believe every single employee and individual should be confident that their working environment is safe and secure. In view of this, we have a responsibility to our 128,000 direct employees, our contractors and suppliers, and our local communities around the world.
To build a true safety culture requires trust and transparency between leaders and employees – we rely on everyone to look out for each other and be “ALL IN! for Safety”.
Laura Ambrose, Chief Safety, Health and Environment Officer
Safety is integral to our culture and is at the forefront of all our activities. Our 2024 campaign for UN World Day for Safety and Health at Work raised awareness of road safety amongst our own employees as well as third party logistics providers who transport our products and brands.
In 2024, we are continuing our Together for Safety programme, which invites our top leaders, including our CEO, to visit one of our manufacturing sites and focus specifically on safety.
Our safety performance reflects the success of our safety-related programmes and policies. We are always striving to improve our safety record and a recent area of focus has been machine safety as this is a key contributor to our Total Recordable Frequency Rate (TRFR). A task force was set up to improve machine safety through the introduction of specific standards and training, and by upgrading our machine guards. As a result of these initiatives, we have seen recordable incident rates reduce significantly.
Our partnerships ensure that we use our influence to improve safety in both the wider community as well as throughout our own operations. Every day, around 18,000 trucks are on the road delivering our products to customers. Incidents not only cause delays and damages, but also cause harm to people. Our Drive to Zero Road Safety is enabled by technology and focuses on six high risk countries. As a result, we have recorded a significant reduction in road fatalities within these countries in 2023 versus 2022.
Safety: a human right at the heart of our business
Health and safety is one of our eight salient human rights issues. We are committed to providing a safe and healthy work environment for all employees as part of our Code Policy on Occupational Health & Safety which forms part of our Code of Business Principles (PDF 5.39 MB).
These safety standards are also based on mandatory requirements which align with the obligations set out in the international standard for occupational health and safety management, ISO 45001. All standards and guidelines are available to our employees on our intranet. Our Code of Business Principles is reviewed regularly, and along with our employees, we expect all others who work with us to follow the principles set out.
The Board’s Corporate Responsibility Committee (CRC) oversees Unilever’s conduct as a responsible business and reviews our Code of Business Principles to ensure that these remain fit for purpose. The Committee also reviews health and safety strategies and performance through a quarterly scorecard.
Our leaders are responsible for cascading and implementing occupational health and safety among their direct reports and third parties within their remit. We also expect all employees to take responsibility for their safety and those around them by acting in accordance with our Codes. In our own operations, we aim for Zero Harm, which underpins everything we do as a business.
Our work with suppliers to improve safety standards can be found in our Human Rights reports and Human rights in our value chain. If an employee is in breach of our safety standards or procedures, cases are dealt with fairly and objectively. Our consequence management policy varies between the countries in which we operate, reflecting local legislation and frameworks. We can take a range of disciplinary actions against those responsible for poor safety oversight, including dismissal in the most serious cases.
Our safety performance in 2023
We report safety data from 1 October to 30 September annually. Our key metric is Total Recordable Frequency Rate (TRFR) which measures the number of recordable accidents per million hours worked. Our TRFR ending 30 September 2023 was 0.58 accidents per million hours worked, which is an improvement of 13% versus 2022. From 2024, reporting will be by calendar year.
In 2023, a contractor sadly passed away while working at one of our factories. We responded with a full investigation and applied the lessons learned to our sites worldwide to prevent a similar reoccurrence.
0.58Accidents per million hours worked in 2023 (employees and directly supervised contractors)
We want all our employees to feel fully confident about the standards of safety in their working environments, and we continue to review procedures and introduce appropriate measures to minimise risks and prevent accidents. When fatalities do occur, our first priority is to support the needs of the families and team members of the individuals involved, while also working with local law enforcement, communities and regulators to fully investigate the root cause of the incident and determine further preventative measures.
A culture of safety
We take deliberate action to continuously instil a culture of safety across the business.
Our Safety Moments programme helps leaders to reinforce safety principles in their teams and demonstrate their accountability for safety standards – ultimately ensuring that our leaders can ‘walk the talk’ on safety.
A safety moment can take many forms within our business, from Unilever-wide pledges to small reflection groups, where employees can openly discuss safety processes in the workplace. We want to create a culture where everyone feels able to intervene in the interests of safety.
All our safety guidance is built into our Unilever Manufacturing System. Manufacturing sites develop individual plans that drive improvements based on their particular risk profile – such as hazardous substances, and electrical or mechanical risks. This helps to build a strong and interdependent safety culture across all levels of our organisation, all under one framework.
Recognising safety best practice
Our annual Global Safety Awards celebrate the outstanding work of our teams around the world to build a positive safety culture. In 2022, we widened the scope of the Global Safety Awards to include third-party business partners in warehousing, transporter carriers and collaborative manufacturing. In 2023, the Premier Safety award winner was our Beauty & Wellbeing factory in Bydgoszcz, Poland, for consistently high levels of operational safety standards and over 24 years of safe work.
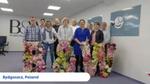
Making the roads safer for everyone
Travel continues to be the highest risk activity involving Unilever employees, third-party suppliers and members of the public. In 2022, we launched a Safe Travel campaign to re-establish the basics around road safety. We also conducted global strategy reviews with the leaders of high-risk countries to advance our best practices.
Our Safe Travel Standard requires that all organisations develop and implement an effective Safe Travel in Vehicles programme, which covers all vehicles purchased or leased by Unilever and all privately owned vehicles driven by our employees on Unilever business. It stipulates the use of telematic devices for high-risk drivers in high- and medium-risk countries to monitor driver behaviour in real time. We believe this is an effective way of reducing road-related incidents and we encourage our business partners to adopt the same measures. We are now looking beyond telematics to more advanced monitoring systems to identify issues such as fatigue while driving.
Improving road safety also includes working with partners outside of Unilever to advocate for a safer working environment and society.
Contractor safety
In the same way as we are focused on providing safer working conditions for our employees, we are equally committed to providing safer environments for our contracting partners on our sites.
Over the last five years, we have strengthened our Construction Safety Programme with initiatives including Construction Safety Standards improvements, Capability Building Workshops, and the deployment of Global Construction Safety Tools.
How we are managing process safety
Process safety governance is driven by Process Safety Steering Committees (PSSC), sponsored by Chief Product Supply Officers and includes Technical Authorities from our Engineering community and Global SHE. Unilever’s key global internal safety standards and third-party Process Safety Management (PSM) audit framework are endorsed by the Committee. These measures support the identification of issues, implementation of action plans and subsequent monitoring of improvements. Issue-specific standards are also in place to support global standards, i.e. hazard-specific standards for individual sites.
As we manufacture a wide variety of products, we have a responsibility to ensure that our operating systems and processes are carefully designed and monitored to protect the people who come into contact with them. Process safety continues to be a key focus area to manage risks in our business and is organised around 12 Process Safety Technical Authorities, with strong governance through the Business Groups. We have also expanded our Technical Authority governance model to upskill employees across all geographies and drive continuous improvement programmes within our factories. The Technical Authorities at various levels have expanded to over 150 across all Business Groups and geographies.
41%Reduction in contractors’ recordable incidents since 2018
Training for everyone, no matter what their role
In 2021, we launched our new Safety, Health and Environment (SHE) Learning Portal, SHEnet, as the one-stop shop for all online and on-demand SHE training. This offers our employees opportunities to develop their safety knowledge and complete certifications. The portal is also used for recording incidents and observations across all our sites which allows us to track safety performance better. In 2022, we continued to develop our content catalogue, including the addition of digitised audits.
For factory employees, safety training starts before they begin their roles. We have a behaviour-based safety programme which is designed to build knowledge and ensure that all employees are committed to helping achieve Vision Zero. This is our company-wide ambition to have no fatalities in our operations.
Our safety performance in detail
We know that some stakeholders appreciate more in-depth disclosure on our safety performance. Below, we provide progress against our preferred accident rate indicator for reporting TRFR for employees since 2010.
The TRFR measures the number of occupational accidents per 1 million hours worked and includes all workplace accidents, excluding only those that require simple first-aid treatment.
The main types of incidents that occur in our manufacturing sites are slips/trips/falls and injuries to hands and arms. In non-manufacturing sites, slips/trips/falls are also the most common type of incident, along with travel-related injuries mainly linked to road accidents.
Accident rates
Year | Total Recordable Frequency Rate per million hours worked |
---|---|
2023 | 0.58 |
2022 | 0.67 |
2021 | 0.55 |
2020 | 0.63 |
2019 | 0.76 |
2018 | 0.69 |
2017 | 0.89 |
2016 | 1.01 |
2015 | 1.12 |
2014 | 1.05 |
2013 | 1.03 |
2012 | 1.16 |
2011 | 1.27 |
2010 | 1.63 |
Notes
In 2013, we adjusted our reporting period from 1 January to 31 December to 1 October to 30 September. PwC has assured our TRFR from 2014 onwards. Since 2019, we have included new acquisitions that operate as decentralised business units in our TRFR; had we included these in 2017 and 2018, our reported TRFR would have been approximately 6% higher in each year.
TRFR is one of two occupational safety performance indicators that has been independently assured by PwC (the other is the number of fatal accidents).
TRFR is calculated as the sum of all lost‐time accidents (LTA) plus restricted work cases (RWC) plus medical treatment cases (MTC), expressed as a rate per million hours worked.
In line with industry best practice, we include temporary staff and contractors who work under our direct supervision in our definition of an ‘employee’, and we capture TRFR for all Unilever manufacturing and non-manufacturing sites (such as offices and research laboratories).
In 2023, the total hours worked equalled 293,802,554.
Fatal accidents
Year | Employees off-site | Employees on-site | Contractors on-site |
---|---|---|---|
2023 | 0 | 0 | 1 |
2022 | 0 | 1 | 0 |
2021 | 2 | 2 | 3 |
2020 | 1 | 0 | 2 |
2019 | 2 | 0 | 2 |
2018 | 0 | 1 | 0 |
2017 | 1 | 0 | 0 |
2016 | 1 | 0 | 3 |
2015 | 1 | 0 | 1 |
2014 | 1 | 0 | 3 |
2013 | 0 | 0 | 1 |
2012 | 3 | 0 | 1 |
2011 | 0 | 2 | 1 |
2010 | 0 | 2 | 1 |
Notes
In 2013, we adjusted our reporting period from 1 January to 31 December to 1 October to 30 September.
Fatalities is one of two occupational safety performance indicators that has been independently assured by PwC. The other indicator is TRFR.
Lost-Time Injury Frequency Rate
Alongside monitoring accidents, it’s vital we analyse their frequency and the nature of any injuries. Our internal reporting system helps us collect more granular data on our Lost-Time Injury Frequency Rate (LTIFR).
LTIFR measures injuries per million hours worked (from 1 October to 30 September). It counts all ‘lost-time’ safety injuries, i.e. injuries that keep people away from work even for one day.
We measure LTIFR for all our direct employees. For the purposes of reporting, we also include contractors under our direct supervision within our direct employee numbers (these are typically the contractors who work on our production lines). We improved LTIFR to 0.23 injuries per million hours worked in 2023.
We also report the contractors who do not work under our direct supervision (who typically provide project or business support). We have been using our internal system to help improve safety for these contractors.
| 2014 | 2015 | 2016 | 2017 | 2018 | 2019 | 2020 | 2021 | 2022 | 2023 |
---|---|---|---|---|---|---|---|---|---|---|
Direct employees (and contractors under direct supervision) | 0.51 | 0.59 | 0.51 | 0.53 | 0.37 | 0.38 | 0.29 | 0.24 | 0.25 | 0.23 |
Contractors (not under direct supervision) | 0.96 | 0.63 | 0.57 | 0.56 | 0.47 | 0.50 | 0.43 | 0.43 | 0.21 | 0.28 |
Occupational Illness Frequency Rate
Our occupational health programmes cover the prevention of work-related illness and occupational diseases, ergonomics, environmental health and protection from noise and enzymes. See Employee health and wellbeing for more information.