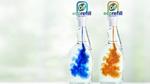
Our progress on plastics
Last year we pledged to make significant cuts to the amount of virgin plastic in our portfolio. Here’s what we’ve achieved since then – plus our plans to do much more.
Unilever GlobalChange location
In another step to help tackle the impact plastic has on the environment, we have developed new containers and lids for our Knorr bouillon powder which are fully recyclable and made with recycled polypropylene plastic (rPP).
The advanced recycling technology that makes this possible transforms low quality, mixed plastic waste that would otherwise be destined for incineration or landfill.
What’s more, the rPP can be re-processed infinitely, as the closed-loop recycling method preserves the quality of the material, thus reducing the need for virgin plastic.
We’re aiming to produce about 1 million of these containers. That equates to saving approximately 2,000 tonnes of virgin plastic in Europe.
“Our goal is to continue making our packaging more environmentally conscious – especially in the food segment – without consumers having to lower their standards in terms of design, performance, user-friendliness and food safety,” says Mike Ross, Senior Packaging Manager at Unilever.
“Unilever is committed to cutting our use of virgin plastic in half by 2025. Turning plastic waste into circular polymer will help meet that goal. We are now testing this using material produced from 100% certified circular polymer, with the goal of expanding across our portfolio by 2025.”
The rPP used in the new Knorr containers is the product of an innovative recycling process from our partner SABIC, a global leader in diversified chemicals. The process transforms the plastic waste into a resin with the same characteristics as virgin food-grade resin. It is not currently possible to produce food-grade rPP with any other form of recycling system.
Our other partner in this initiative, Greiner Packaging – a leading European manufacturer of plastic packaging – takes SABIC’s rPP and uses it to produce the new recyclable packs.
The appearance, functionality and safety of the new packaging are the same as before and the quality is as high as ever.
So, nothing has changed from the consumer’s perspective. They can still simply remove the cardboard sleeve from the container when it’s empty, then recycle the two components as usual. Alternatively, as the containers are resealable and dishwasher-safe, they can be reused to store food either at home or for day-to-day use in the food service industry.
In August 2019, Magnum became the first ice cream brand to use food-grade recycled plastic made with SABIC’s technology, launching 600,000 of its new tubs in Belgium, the Netherlands and Spain. This year, we have introduced more than 7 million into other European countries. And from next year, we’ll be rolling them out globally.
These new packs from Knorr and Magnum contribute to our wider global packaging commitment to halve our use of virgin plastic by reducing our absolute use of plastic packaging by more than 100,000 tonnes and accelerating our use of recycled plastic by 2025.
Last year we pledged to make significant cuts to the amount of virgin plastic in our portfolio. Here’s what we’ve achieved since then – plus our plans to do much more.
Today we launch a range of ambitious new commitments and actions to fight climate change, protect and regenerate nature, and preserve resources for future generations.
Until now, black plastic bottles have been impossible to mechanically detect and sort for recycling. But we’ve developed a way of doing it. And we’re making the technology and approach available to everybody.
Have you got a few minutes to complete a survey? We would love to hear about your experience using Unilever.com.