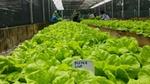
Ten years ago, Unilever committed to making sustainable living commonplace through the Unilever Sustainable Living Plan. This meant looking at the impact of our products across our value chain – including how they were designed, sourced and made.
In supply chain, our goal was to transform our manufacturing processes, from ensuring environmental care through compliance, measuring our impact on the planet and minimising overconsumption and inefficiencies in energy, water and waste.
This has enabled us to reduce our carbon footprint; to replace fossil fuels with green forms of energy; to find ways to source and reuse water; and to journey towards a waste-free world. In short, to build sustainability into our manufacturing DNA.
It has taken commitment, ingenuity and hard work by thousands of people across our manufacturing supply chain.
We’ve captured just a few of the stories highlighting the progress our factories have made in the past decade in a short film – from achieving 100% renewable energy use (and in some instances generating surplus power for the markets and communities we serve) to finding smart ways to harvest rainwater to create a more secure water supply for factory use.
We continue to set bold targets
And our ambition does not stop there. We continue to set bold targets. We want our operations to have zero emissions by 2030. We are working hard to protect water. Since 2010 we have reduced consumption by 47% and, as part of our new commitments, are implementing water stewardship programmes for local communities, intended to reach 100 locations by 2030.
As we transition from eco-efficiencies to absolute zero, we will be adopting more circular models. We will bring circular economy principles into the mainstream, with designs and implementations that reuse, recycle and recover material and maximise value from unavoidable waste operations.
A global effort to create change
“What amazes me is the global effort that has come together to deliver an astonishing change in the sustainability area,” says Head of Sustainable Manufacturing Helen Hudson.
“We’ve really mainstreamed the words sustainability and environment and put them as part of our priorities in terms of how we work in our factories. And now we are talking about how we do it more, and that’s brilliant,” she says.
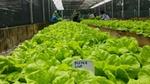
1.Turning factory waste into fresh vegetables (1 of 3)
Our Pouso Alegre site in Southern Brazil employs more than 1,100 people and manufactures some of our leading food brands. It’s also Unilever’s first zero carbon operational site in the Americas. Environmental Co-ordinator Rodrigo Cano was one the key people behind a project at the site, called Ecologica Island. Using the principles of circular economy, the team built two 500 sq m greenhouses and used the factory’s plant-based waste to enrich their soil. Both greenhouses now grow vegetables and yield enough produce to supply the factory’s restaurants two days a week.
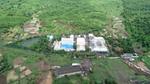
2. Harvesting rainwater to secure a factory’s water supply (2 of 3)
Unilever’s Dapada site in India manufactures soap and detergent for millions of consumers. The country’s monsoon season runs from May to September and accounts for 70% of its annual rainfall. It’s often followed by prolonged dry spells that quickly lead to water shortages. To ensure a more secure water supply for the factory, Akshay Rastogi, Factory Manager at Dapada, along with the team, built a rainwater harvesting pond on the site. It is surrounded by trees, which reduces water evaporation during dry spells.
The build means 75% of Dapada’s water consumption now comes from rainfall, which ensures traditional water supplies such as rivers and streams can be more fully used by the local community.
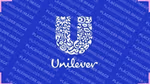
3. Creating a fossil-free energy contract (3 of 3)
Flen in Sweden was our first site to achieve carbon neutral status. In 2011, it switched its energy use to 100% renewable electricity. “In 2010 our factory had a carbon footprint of 870 tonnes,” says Igor Papec, Factory Leader at Flen. “Today we have a zero carbon footprint. Our energy intake is completely green and comes from solar, wind or hydropower – energy sources with an extremely low-carbon footprint which provide us with a climate-smart solution.”
The site created a fossil-free energy contract with its energy supplier, ensuring that its power only came from renewable sources from the national grid. “We wanted to show people, the community and government that things can be done if you seriously put the effort in,” Igor says.
The imagery used in this film was shot before the COVID19 pandemic.
Any subsequent work followed Unilever’s COVID19 safe guidelines.
Related articles
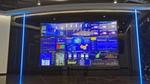
Hefei joins 'Lighthouse' network of world's most digitally advanced factories
Our Hefei site in China has become our second facility in nine months – alongside the Dubai Personal Care factory – to join the World Economic Forum’s network of Lighthouse factories, shaping the future of manufacturing through digital technologies.
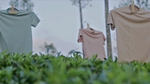
How a tea stain turned into a fashion opportunity
Waste from our Ceytea factory in Sri Lanka is being transformed into a suite of natural fabric dyes that are providing the fashion industry with greener alternatives
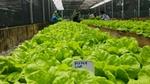
Composted factory waste feeds a garden that feeds a community
When the team at our Pouso Alegre site in Brazil realised that they could speedily turn its organic waste into compost, the idea of a factory garden followed. Its fresh produce is served in the staff café and at a local nursery and residential home